
Helmet Safety Standards 2019: Times – and Standards – They are a-changin’
“There is no cure for brain injury. A brain injury is forever. We can teach someone strategies for dealing with the handicaps, but the only effective approach in dealing with head injury is prevention…not to let the injury occur in the first place.”
-William D. Singer, M.D., Harvard Medical School, as quoted in UNECE report #29 entitled, “The United Nations Motorcycle Helmet Study” 2016. (ISBN 978-92-1-117107-5)
Back in 2013, we offered you a comprehensive look at some of the most common helmet safety standards that manufacturers using to certify the safety of their products.
That article has been the subject of a lot of reader interest, and we hope it has been helpful to motorcycle riders considering their helmet options.
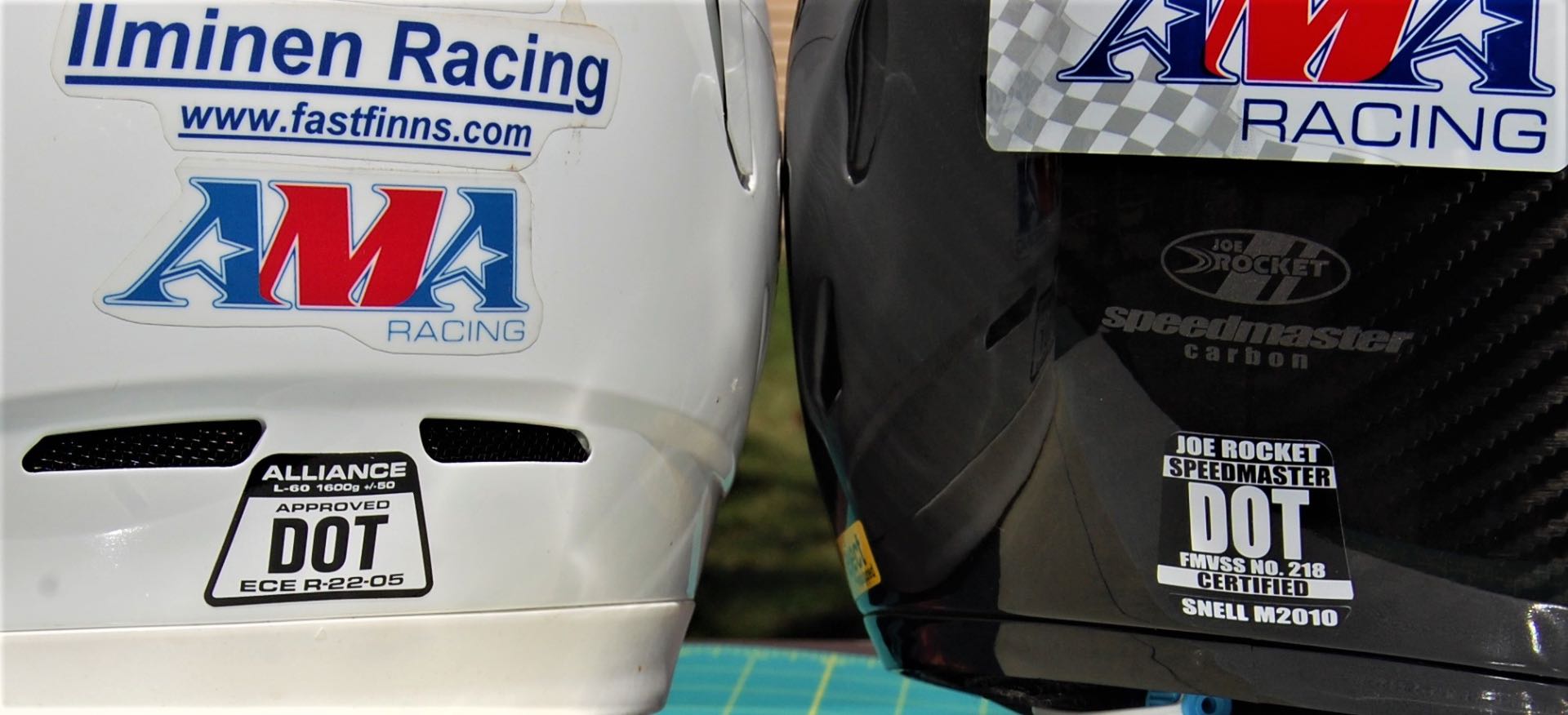
For 2019, quite a few things have changed and others have stayed the same. Now there may be a whole new factor for potential helmet-buyers to consider.
With that said it may be a good time to give the subject of helmet safety standards a fresh look. It is important to remember that not all standards discussed here are mandatory, and any given helmet may be certified under more than one standard allowing it to be sold in a range of countries around the world as well as in the United States.
The most notable recent development in the progression of helmet safety performance standards is the entry of the Fédération Internationale de Motocyclisme (FIM) into the mix of organizations promulgating helmet standards for use in MotoGP, Moto2 and Moto3 and all other FIM-sanctioned competition, starting with circuit racing in 2019.
Beginning with stakeholder meetings held in Germany in 2016, the FIM Helmet Certification Programme (FHCP) proposal was presented. Development of the technical details continued from that point on.
The FHCP was established, with the collaboration of the helmet manufacturers and other stakeholders in order to define a new test standard that goes above and beyond existing ones (e.g. UN ECE 22.05, Snell M2015, JIS T8133), which FIM has recognized for use in competition previously.
Note that the U.S. federal helmet safety standard referred to as “DOT” based on Federal Motor Vehicle Safety Standard 218 (FMVSS 218) was not included as it has never been recognized by FIM for competition use.
Interestingly, the FIM test protocols borrow from the other sets of standards for various aspects of homologation testing. The FIM explains the program this way:
“In order to take account of a more complete and demanding evaluation of performance, and give specific and exclusive recognition to helmets that meet more demanding criteria, the FIM Technical and Circuit Racing Commissions have now launched a pioneering and unique program, the FIM Racing Homologation Program for helmets (FRHPhe), which features the latest state of the art methods of testing.
“Under this program, the FIM grants helmets a homologation certificate and labels, which are a mandatory prerequisite to be entitled to access FIM Circuit Racing competitions.
“The FIM Homologation Label to be affixed to the helmet’s chin strap will uniquely identify each helmet approved for use in FIM Grand Prix competitions with a serial number and will be verified by FIM Technical Stewards. By scanning the label QR code, information relative to the helmet features and the validity of the homologation will be immediately accessible. A link to the manufacturer webpage will be also available for redirection to the advertising and the web services offered by each manufacturer. The 3D FIM hologram will add a high security value to the label to make use of any helmet not actually approved under the FIM standards difficult.
“To obtain such homologation, the helmet has to meet the high performance and quality standard set by the FIM, in addition to being approved according to selected international standards.
“The helmet properties are evaluated through a test protocol which aims to trigger the development of helmets offering an optimal protection for riders. An optimal protection is understood as providing a minimized risk of skull fracture and of the multiple forms of brain damage, as well as a measured and controlled mechanical performance of the protective padding and the shell.”
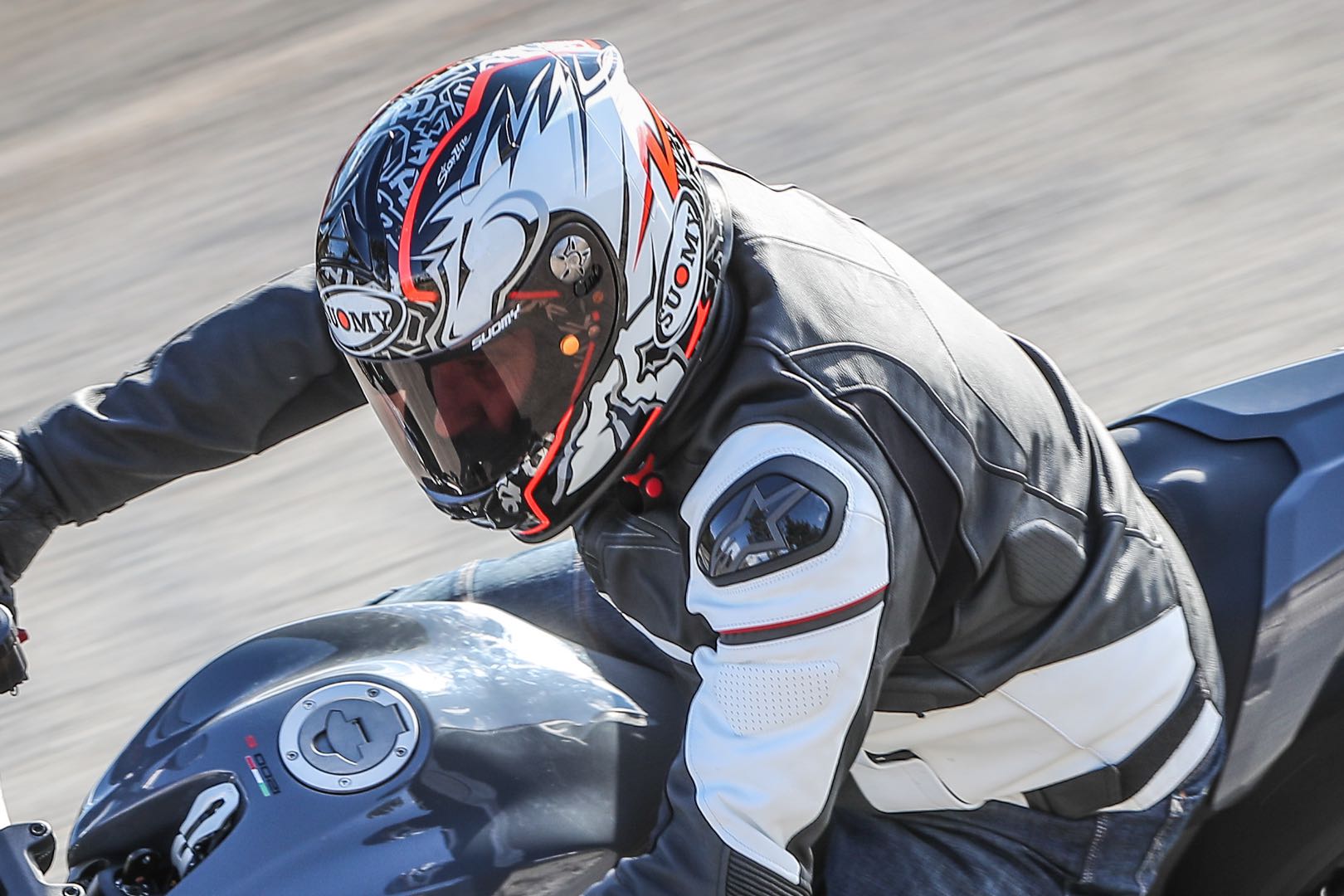
The following helmets are eligible for qualification under the FIM standard (Note that this indicates the FIM standard aligns with several of the existing standards in various aspects of testing, but each type listed would still have to be submitted for individual helmet make/model testing by FIM’s designated test lab before it could be approved for use in FIM-sanctioned competition):
ELIGIBLE FIM HELMETS
- UNECE 22.05 Type P (full-face)
- Snell M 2015 compliant
- JIS T8133 2015 Type 2 Full face
- Protective lower face cover: not detachable and not moveable and made of the same material as the shell
- One-piece shell
- Retention system with strap and double D-ring closure
Helmets submitted for testing must also include any accessories intended to be used with the helmet in competition. At present, the testing regime does not include any testing of the face shield under the FIM standard, however face shield testing is included under ECE 22.05.
The qualification testing utilizes a random sampling of ten production helmets as described by FIM to include:
FIM Helmet Sampling Test
- Samples #1, #2 and #3: Conditioning, Weight, Linear impact tests
- Samples #4 and #5: Conditioning, Weight, Oblique impact tests
- Sample #6: Conditioning, Weight, Penetration tests
- Sample #7: Storage
- Sample #8, #9 and #10: Conditioning, Weight, Extra tests if needed
The helmets are homologated per size and per declared combination of accessories (e.g. aerodynamic devices).
Testing specifications:
FIM Helmet Linear Impact Test
The FIM test approach first assesses the helmet response to very high and medium-low severity linear impacts, randomly in 13 out of 22 pre-established locations distributed all over the helmet surface. This aims at evenly assessing the level of protection against skull fracture and at assessing the mechanical properties of the protective padding (or liner).
Helmet sample #1 (HIGH SPEED UNECE POINTS—Points refers to impact points on the helmet shell)
- As defined in UNECE 22.05 (Impact-absorption test, more on the ECE 22.05 test specs follow), with flat anvil only
- UNECE points B, X, P, R: impact velocity: 8.2 (+0.15, -0.0) m/s (meters per second)
- UNECE point S: impact velocity: 6.0 (+0.15, -0.0) m/s
Helmet sample #2 (HIGH SPEED EXTRA POINTS)
- As defined in UNECE 22.05 (Impact-absorption test), with flat anvil only
- 3 “extra” points (selected among 12 pre-defined points): impact velocity: 8.2 (+0.15, -0.0) m/s
Helmet sample #3 (LOW SPEED UNECE POINTS)
- As defined in UNECE 22.05 (Impact-absorption test), with flat anvil only
- UNECE points B, X, P, R, S: impact velocity: 5.0 (+0.15, -0.0) m/s
The test criterion that is unique to the FRHPhe homologation requirements is the addition of oblique or angular impact testing. This aspect of testing is intended to address the helmet’s effectiveness in mitigating rotational impact forces. FIM criteria describe it as follows:
FIM Helmet Oblique Impact Test
“The FIM test procedure pioneers the assessment of the helmet response to medium severity oblique impacts, aiming at evaluating the level of protection against brain injuries generated by critical rotational accelerations.
“The oblique test constitutes the most novel and modern aspect of the methods of testing and reflects a very common scenario occurring in real world accidents, although never addressed in international standards so far.”
- Helmet sample #4 (points 45, 180 and 270 degrees)
- Helmet sample #5: points 0 and 135 degrees
As defined in UNECE 22.05 (Impact-absorption test), with: platinum cure silicone coated headform (µ = 0.78), “oblique anvil”: 45º plane, abrasive paper to be substituted after significant damage, impact velocity 8.00 (+0.15, -0.00) m/s. The test is intended to impart rotational force and measure its severity as transferred to the headform inside the helmet.
FIM Helmet Penetration Test
In addition, a penetration test is included in the protocol and used to check the shell resistance to impacts against sharp objects.
- As defined in JIS T8133: 2007 5.2 and 7.5 (Type 2), with:
- spherical support
- dropping height: 2m
- 2 penetration sites, above the Snell “test line”, at least 75 mm separated
Performance Thresholds under FIM Standards:
Samples #1 and #2 (Linear impact) |
|
Sample #3 (Linear impact) |
|
Sample #4 and #5 (Oblique impact) |
|
Sample #6 (Shell penetration) | No contact between striker tip and support surface |
Unlike U.S. DOT FMVSS 218, no “self-certification” is allowed. All helmets must be tested by a public or private independent testing lab assigned by the FIM. At present, the only testing lab recognized by the FIM is the Impact Laboratory of the Aragon Institute of Engineering Research (University of Zaragoza) in Spain.
A number of helmet manufacturers have already completed the approval process, have completed testing and approval is pending or have testing in progress:
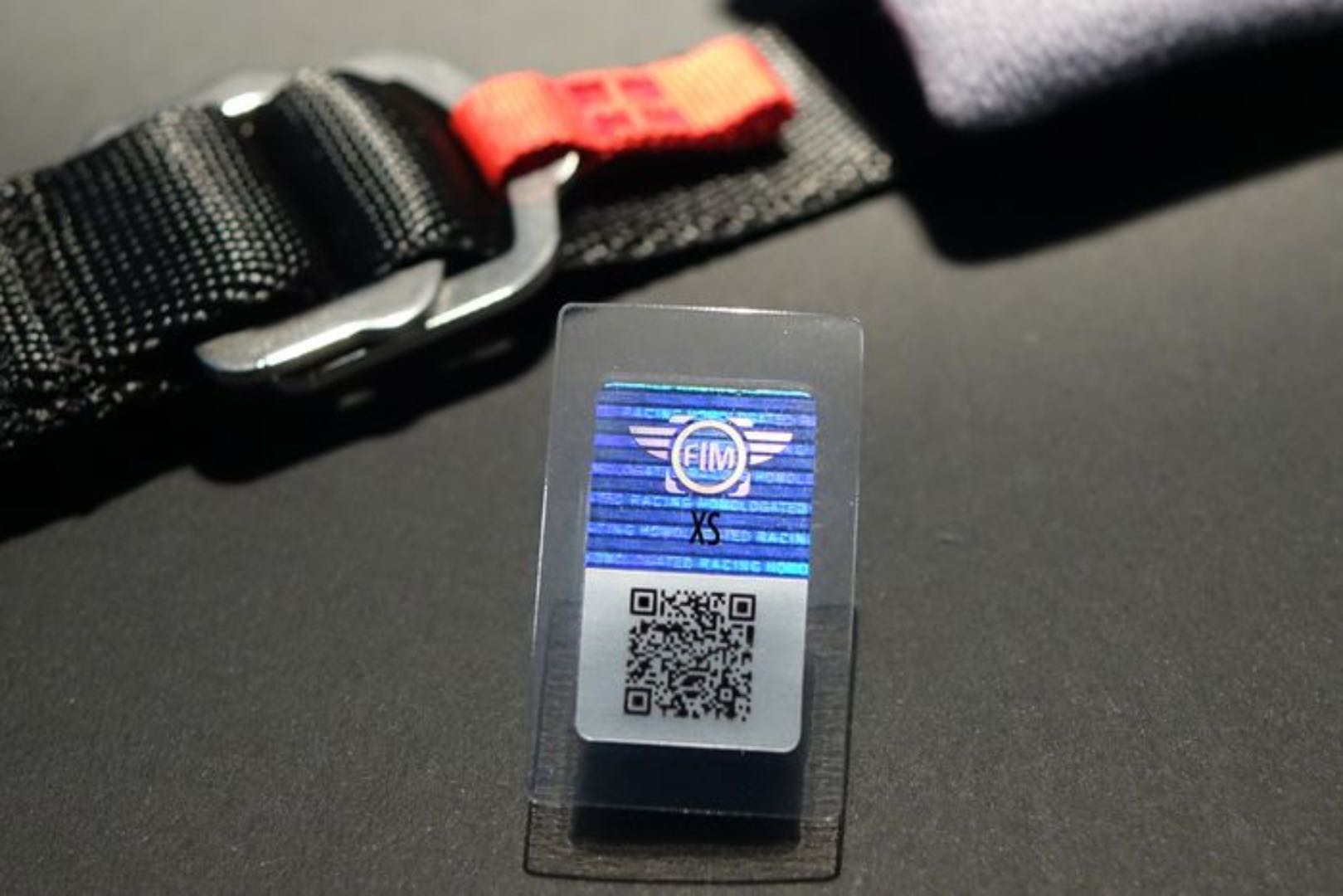
FIM homologation completed (as of January 25, 2019)
- Shark Race R Pro GP sizes XS-XL FRHPhe-01 2018
- Bell Pro Star ECE sizes S, M, L FRHPhe-01 2018
- AGV Pista GP R sizes S to MS FRHPhe-01 2018
Passed homologation tests – FIM homologation pending (as of January 25, 2019)
- ARAI – RX-7 Racing (without aero-device) – sizes XS, S, M, L
- HJC – RPHA 01R – sizes XXS, XS, M
- KABUTO – RT-33 – sizes M, L, XL
- SCORPION – EXO-R1 FIM Racing #1 – size S
- SHOEI – X-Fourteen – sizes XS, S, M
Homologation tests pending (as of January 25, 2019)
- 6D
- AIROH
- ARAI (RX-7 Racing with aero-device and RX-7V Racing)
- HJC (size S)
- LS2
- MT
- NHK
- NOLAN/X-LITE
- SCORPION
- SUOMY/KYT
FIM-Sanctioned events where use of FRHPhe helmet homologation is required:
- FIM Grand Prix World Championship
- FIM Superbike World Championship
- FIM Supersport World Championship
- FIM Sidecar World Championship
- Red Bull FIM MotoGP Rookies Cup
- FIM Supersport 300 World Championship
- FIM CEV Repsol Moto3 Junior World Championship
- FIM World Record Attempts
- FIM Drag Bike World Cup
- FIM Endurance World Championship
- FIM Endurance World Cup
Perhaps the most useful information to take away from this quick overview is how the FRHPhe helmet homologation standards will reduce the allowable amount of impact (g) force—deceleration—to reach the wearer and also call for reduced head injury criterion (HIC) values in linear and oblique impact testing.
The lower those values are, the more impact energy the helmet has absorbed, preventing it from being transmitted to the wearer’s brain and the lower the potential for brain injury. The impact energy attenuation standards shown for implementation in 2020 are by far the most aggressive performance standards in any of the systems to date.
Stay tuned to Ultimate Motorcycling for continuing updates and details as the new FRHPhe helmet homologation standards move into the implementation phase. It is important to remember that for helmet buyers, the new FRHPhe is not mandatory unless you are planning to participate in FIM-sanctioned racing events. In that case, you must have a helmet the bears the FRHPhe label.
Reference: FIM: http://www.fim-live.com/en/
DOT (U.S. Department of Transportation FMVSS 218)
If you are in the market for a helmet in the U.S. and some parts of Canada for use on public roads, any helmet sold for that purpose must bear the latest version of the DOT certification label.
Indeed, little apart from those label requirements that were revised in 2013 in the hope of making sale of non-DOT approved helmets more difficult, has really changed with the requirements for performance in the DOT standards.

The impact attenuation performance, retention system and other requirements have not changed since 2013 although a clarification on helmet retention strap testing method was issued in 2015.
In an effort to make counterfeit labeling of non-compliant helmets more difficult and legally risky to those who do it, the DOT label displayed on the back of the helmet was changed to include the following, in order from top to bottom:
The manufacturer’s name
- Model number or name
- “DOT” below the manufacturer’s name
- “FMVSS 218” centered below DOT
- The word “Certified” below FMVSS 218
The National Highway Traffic Safety Administration (NHTSA) has enforcement authority for the DOT certification requirement, which applies to helmets intended to be sold for on-road use. Of course, using a helmet certified under at least one of the sets of standards for off-road purposes or in competition makes sense.
Unlike FIM, ECE and Snell, NHTSA does not test helmets against the DOT standards, nor does the regulation require the manufacturer to submit production helmets to any independent test lab for evaluation before they can claim DOT standards compliance.
Each helmet manufacturer marketing their helmets for road use in the U.S. is allowed to test and self-certify the models they want to sell and then permanently affix the “DOT” emblem signifying compliance with FMVSS 218. NHTSA enforces the standards by having a third-party testing lab acquire samples of selected products to verify compliance. Penalties to manufacturers for marketing non-compliant products can be steep—up to $5,000 per helmet.
If self-certification sounds a bit weak, there is no set minimum number of helmets specified in the DOT standard that must be tested by NHTSA’s contracted lab from each manufacturer, either.
In December, 2018, ACT Lab, a California-based independent ISO 17025 accredited laboratory that conducts safety and compliance testing for the motorcycle, bike and outdoor industries, was awarded a 5-year contract from the National Highway Transportation Safety Administration (NHTSA) to conduct helmet testing.
ACT Lab then purchases specific helmets identified by NHTSA through retail channels. This is to eliminate any possibility of manufacturer sample selection. ACT Lab tests them, and provides results data to NHTSA—not the manufacturer. This is what is known as “post-marketing” testing, and while it may lead to removal of non-compliant helmets after they reach some consumers, the approach does not prevent that from happening in the first place.
FMVSS 218 sets standards in three areas of helmet performance: impact attenuation (energy absorption); penetration resistance; and finally the retention system effectiveness. The standard requires peripheral vision to be not less than 105° from the helmet midline. Projections from the surface of the helmet (snaps, rivets, etc.) cannot exceed 5 mm.
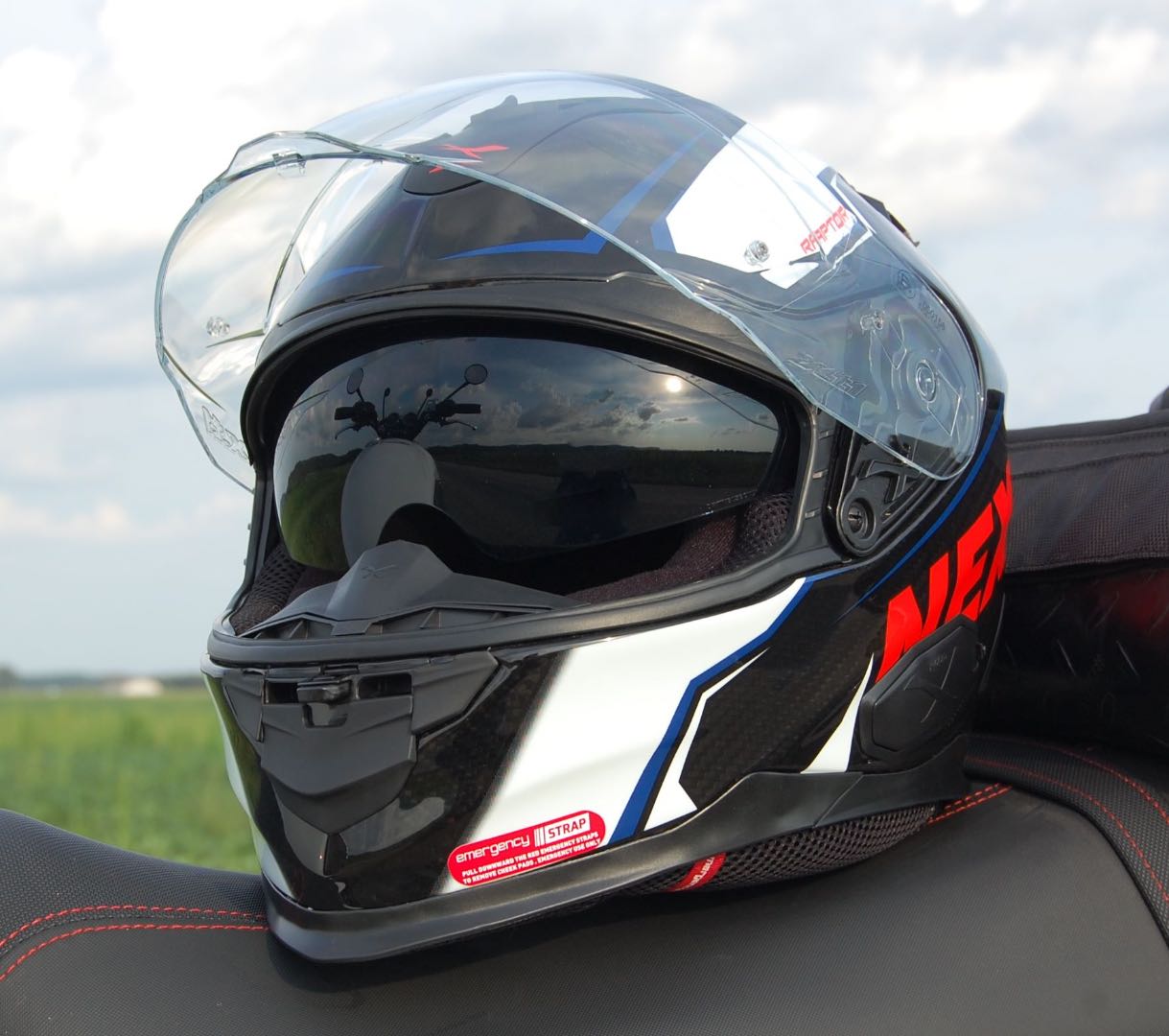
As is the case with other test systems, impact testing measures acceleration of a headform inside the helmet when it is dropped from a fixed height onto a spherical and flat surfaced anvil. The standard allows a peak acceleration energy of 400 G (G being “gravity constant” or an acceleration value of ft. per second x seconds). Accelerations in excess of 200g shall not exceed a cumulative duration of 2.0 milliseconds; and accelerations in excess of 150g shall not exceed a cumulative duration of 4.0 milliseconds.
The penetration test involves dropping a piercing test striker onto the helmet from a fixed height. The striker must not penetrate deep enough to contact the headform.
The retention system test involves placing the helmet’s retention straps under load in tension. For this test the load is progressive; first a load of 50 lb. is applied for 30 seconds, then it is increased to 250 lb. for 120 seconds, with measurement of the stretch or displacement of a fixed point on the retention strap from the apex of the helmet.
Reference: NHTSA, https://www.nhtsa.gov/
United Nations ECE Standard 22.05
ECE stands for “Economic Commission for Europe,” which was created under a United Nations agreement in 1958. In our 2013 coverage of helmet safety standards, we included fairly detailed information about how helmets were tested for compliance with that standard.
Below is a general description of the most recent updates to ECE 22.05 standards as presented in the UNECE report #29 entitled, “The United Nations Motorcycle Helmet Study” 2016. (ISBN 978-92-1-117107-5). The ECE 22.05 standard is now recognized by 62 countries around the world including many outside the European Union, but not by the United States.
Helmet configurations under the ECE 22.05 approval regime are designated by the following codes:
- “J” if the helmet does not have a lower face cover (3/4 coverage open face & half-helmets)
- “P” if the helmet has a protective lower face cover (full-face fixed chin bar and modular), or
- “NP” if the helmet has a non-protective lower face cover. If fitted with a non-protective lower face cover the outer surface of the cover must be marked “Does not protect chin from impacts” and/or with a symbol indicating the lower face cover does not offer any protection against impacts to the chin.
The general requirements include:
- Requirements on the basic structure, visors, peaks and the need to identify non-protective chinstraps;
- Much more detailed requirements concerning the extent of the helmet’s head coverage;
- The same requirements remain in effect for hearing and ventilation;
- The introduction of shear testing for helmet shell surface irregularities of over 2 mm in height, requirements to smooth projections, and controls on the interior surface of the helmet shell (i.e. no projections);
- For chinstraps there are requirements regarding protection from abrasion, the minimum width of the chinstrap, adjustment devices, positioning of the fastening/tensioning devices, and latching and release of fastening systems. The requirements also ban chin cups;
- The extent of peripheral vision (105° from the helmet midline), which should be tested by a field of vision test;
- Requirements for material durability;
- General specifications for the visor, e.g. removability, specifications for devices for lifting the visor out of the line of sight with one hand;
- Provisions for child helmets (introduced in 1983 with 2002 series of amendments).

Specific tests for the helmet have been updated and new tests added as follows:
- Conditioning procedures have been extended to include ultraviolet conditioning and solvent conditioning (for hydrocarbons, cleaning fluids, paints, transfers or other extraneous additions that may affect the shell material);
- The impact-absorption test is based on the measurement of the deceleration of a head. The Head Injury Criterion (HIC) is calculated for five specific test points (including the protective chinstrap) using a guided free fall helmet drop test. The absorption efficiency shall be considered sufficient where the resultant acceleration measured at the center of gravity of the headform (placed inside the helmet to simulate the wearer’s head) at no time exceeds 275 g, and the Head Injury Criterion does not exceed 2400.
- The new test for surface friction measures the rotation-inducing forces created by projections, e.g. visor fittings, studs, etc., and friction with other surfaces. The rotation-inducing forces caused by projections on the helmet and friction against the outer surface of the helmet which occur when a helmeted headform is dropped vertically on to an inclined anvil are measured in the longitudinal axis of the anvil. The drop height is such that the unit constituted by the headform and helmet falls on the test anvil at a velocity which, immediately before impact, is equal to 8.5 m/s.
- The rigidity test remains the same. The helmet is placed between two parallel plates and a known load is applied along the longitudinal axis or the transverse axis. An initial load of 30 N (Newtons) is applied, at a minimum plates speed of 20 mm/min, and after two minutes the distance between the two plates is measured. The load shall then be increased by 100 N, at a minimum plates speed of 20 mm/min, and then wait for two minutes. This procedure is repeated until the application of a load of 630 N is reached. In the test along each axis, the deformation measured under the 630 N load must not exceed that measured under the initial 30 N load by more than 40 mm.
- The new dynamic test of the retention system assesses the displacement of the retention system under a dynamic and then, over time, a static load;
- The new retention (detaching) test checks whether the helmet is likely to “roll” forward and off the head if struck from behind;
- The new test for the micro-slip of the chinstrap checks how much slip occurs when the strap and fastening are placed under variable loads (as when wearing the helmet);
- The tear test of the strap has been replaced by an abrasion test in which after an abrading procedure, the strap is tested under tension;
- For the new quick-release mechanisms, tests are performed for accidental operation, ease of release, and durability. This includes a test where the release is closed and locked. Then the procedure is to apply a loading force of 20 ” 1 N in the direction in which the mechanism is designed to bear load, then unlock and disengage the mechanism under load. This cycle is completed in not less than 2 sec and is repeated 5,000 times. For mechanisms containing metal components, this test is conducted after exposing the release mechanism to a corrosive solution for a prescribed amount of time.
With the introduction of visors, a new series of tests was developed:
- Prior to any other tests a general ultraviolet conditioning test should be performed;
- The mechanical impact visor test checks for sharp splinters after impact—the test specifications even define how to determine if a splinter is “sharp”;
- Light transmission through the visor is tested and there are specifications for tinted visors that may only be used in daytime;
- Light diffusion, i.e. the scatter of light towards the eye, is checked as are spectral transmittance and refractive powers;
- The scratch resistance test measures the light diffusion after the surface has been abraded, e.g. the “starring effect” from headlamps;
- Recognition of signal lights (not necessary if the transmittance value is very high);
- Mist retardant (anti-fogging) properties, if the visor has been so treated, are measured by the degree of light transmission lost due to misting. (Misting has always been a phenomenon with full-face helmets, which is why these kinds of coatings are used and why it must be easy to lift the visor out of the field of vision).
To ensure easy availability of the following information to the helmet user, UN Regulation No. 22 requires the helmets to be labelled with:
- The size and maximum mass;
- Information on the proper attachment and fitting of the helmet
- A reminder to replace the helmet after a violent impact
- A warning against using of a helmet coming into contact with petrol, paints and solvents
- The types of visors approved for use with the helmet.
Non-protective chinstraps must be marked, thus indicating that they have not been tested or have failed to meet the requirements. Visors have to be labelled with the type of helmet to which they can be fitted and they shall be accompanied by information on cleaning, use at night and in poor visibility, and any mist retardant properties.
The helmet shall carry the type approval mark as specified in ECE 22. This mark shows which type approval authority granted the helmet type, the status of the Regulation when it was approved (in the first two digits of the approval number), subtypes and a serial number. The approval mark provides immediate evidence that the helmet has been type approved.
Unlike the DOT system, where the product is not subject to third-party testing prior to sale, the ECE system requires batch sampling when production begins, submission of up to 50 sample helmets/visors to a designated laboratory working for the government that uses the ECE standards under the United Nations agreement prior to helmets being offered for sale as compliant with ECE standards and verification of quality control during on-going production.
Reference: UNECE, http://www.unece.org/trans/main/wp29/wp29regs.html
Snell Memorial Foundation M2020D and M2020R
The Snell Memorial Foundation is not a helmet manufacturer, retailer or regulator. It is a non-profit organization established in 1957 to help drive on-going improvement in helmet safety performance through the development of consistent standards and testing methods. Snell certification is voluntary and is not required by federal or international authorities, but may be required by some competition sanctioning bodies.
The M designation on the Snell Standards refers to the standards applicable to helmets for use with motorcycle helmets. The M2020, of August 2018, updates to the Snell standards does create some alignment with other standards, specifically the U.S. Department of Transportation (DOT) standards in FMVSS 218 and the United Nations ECE 22.05. Snell Foundation information explains it this way:
“This M2020 revision of the Snell Foundation standard for motorcycle helmets allows two distinct options: the first is a continuation of the requirements which had been set for M2010 and for M2015. It is designated M2020D indicating compatibility with DOT. It demands the premium levels of impact energy management currently required in M2015. The second incorporates modifications to the impact test requirements to accommodate the greater impact attenuation demanded by European standards. It is designated M2020R indicating compatibility with ECE Regulation 22.”
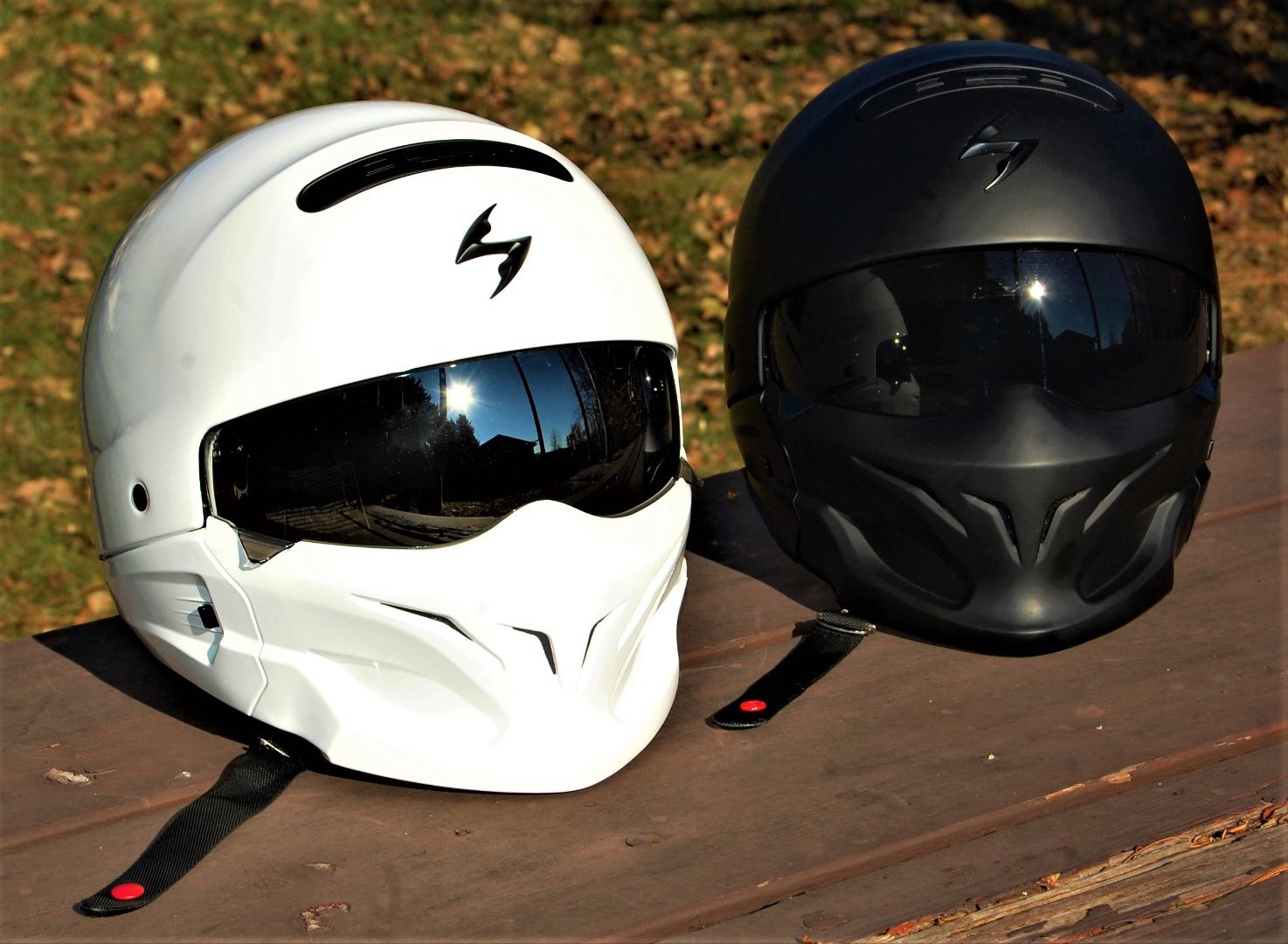
In introducing this approach, the Snell Foundation creates a method that is flexible in allowing helmet manufacturers to design products that will meet applicable standards for marketing their helmets in both the United States and Europe as well as other countries outside the E.U. that recognize ECE 22.05 but not DOT standards.
The conundrum faced by helmet manufacturers by the differences in the applicable performance standards is summed up in Snell Foundation information:
“Only a single helmet maker has been able to obtain European homologation for its Snell M2015 certified helmets while other manufacturers protest that they cannot produce helmets meeting Snell requirements which will also be eligible for use in Europe. Therefore, M2020R is formulated to identify helmets with a premium of protective performance in areas where ECE Regulation 22 homologation is required. It is hoped M2020R will also enable some reasonable compatibility with FIM FRHPhe-01 impact test requirements. The roll-back in test severity enables this compatibility but to assure compatibility, this standard will also impose a HIC criterion in the evaluation of the M2020R impact tests. Although the Snell Foundation’s directors firmly believe that HIC has little value in assessing helmet protective capability, its inclusion in ECE and FIM helmet standards dictate that a HIC criterion be included in M2020R in order to assess compatibility with these mandatory requirements.”
Philosophical differences about the value of HIC criteria in assessing helmet performance aside, the move by Snell signals that even as the range of helmet certification options has widened, the alignment of those standards has a chance to improve.
Snell Foundation testing evaluates each helmet model in several areas and specifications for pre-test environmental conditioning of helmets are used. As with the other systems, 105° of peripheral vision from the midline is required.
There are general requirements for the construction of the helmet. The assembled helmet must have smooth external and internal surfaces. Any feature projecting more than 7 mm beyond the outer surface must be designed to allow it to readily break away; all other projections on the outer surface must be smoothly faired and offer minimal frictional resistance to tangential impact forces.
Rivets and similar projections into the helmet interior must not present a laceration or puncture hazard. Rivet heads cannot project more than 2 mm above the helmet’s surface. Restraint clips may be used at the rear or on the side of the helmet. The helmet must provide as nearly uniform impact protection over the entire protected area as is possible. The standards do not include any requirements or restrictions as to interior helmet ventilation, internal sun shades, finish colors or reflective surfaces or lights that may be included.
The retention system is tested by first applying a 23 kg (50.6 lb.) tension load to the fastened chin strap for one minute, then simultaneously removing that load and imparting a 38 kg (83.6 lb.) guided fall load to the closed strap system. Breakage or deflection of the strap in excess of 30 mm results in failure of the test.
Impact absorption testing is done in similar fashion to ECE and DOT, using a free-fall drop test from a height necessary to attain the specified impact velocity with a head form in the helmet to measure impact energy transferred to the interior of the helmet when dropped on to a fixed anvil. Impact velocities range from 4.84 m/s to 7.75 m/s for M2020D and 4.82 m/s to 8.20 m/s for M2020R.
Three different anvil shapes are used in the testing. The peak acceleration energy allowed ranges from 243 to 275 G with no HIC limit specified for M2020D testing and from 257 g to 275g with HIC limit of 2880 specified for M2020R testing. The height the helmet is dropped from varies; the velocity reached by the impact point is what is specified in the test specifications. Impact testing on full-face helmets is done on the chin bar, as well as other points on the shell and modular helmets are tested with the chin bar locked down and include frontal and lateral impacts.
Protection provided by the helmet shell from penetration is tested by dropping a 3 kg (6.6 lb.) pointed striker on the helmet at a velocity of 7.45 m/s. The helmet fails the test if the striker penetrates the helmet shell making contact with a “tell-tale” markable material applied to the headform.
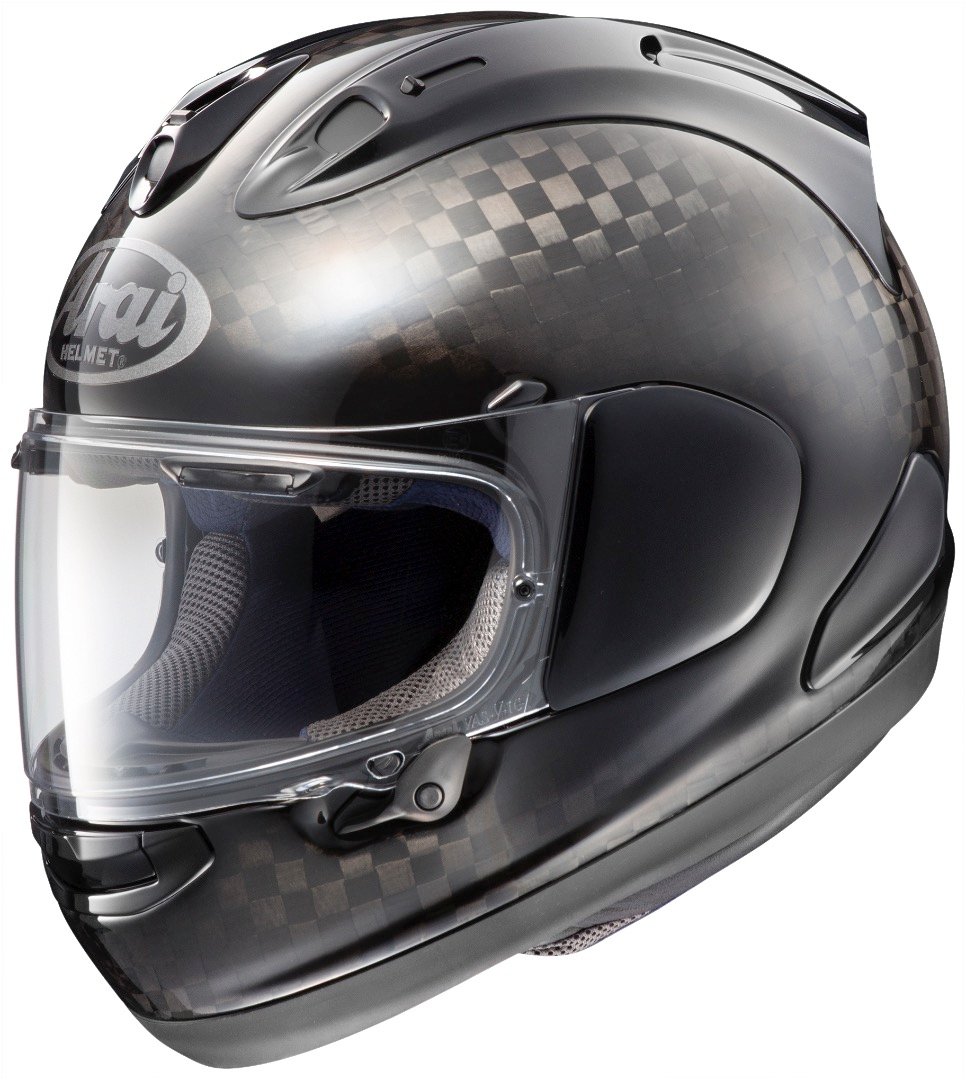
Full face helmets are tested for strength of the chin bar by mounting the helmet chin bar facing up in a jig and dropping a 5 kg (11 lb.) weight with a flat surface onto the chin bar midpoint at a velocity of 3.5 m/s and measuring the amount of deflection the impact causes. Deflection of 60 mm (2.3 in.) or more or failure of the chin bar likely to result in injury to the wearer means failure of the test.
Positional stability or “roll-off” is tested using a 4 kg (8.8 lb.) weight attached to first rear edge of the helmet by a cord with the helmet positioned and properly strapped on a headform facing downward at a 135° angle such that when the weight is released for a free-fall height of 0.6 m, it would tend to try to dislodge the helmet from its correct position on the head form. Then the helmet is rotated 180°, the weight is attached to the front edge of the helmet opening and the test repeated. Failure occurs if the helmet rolls off the head form.
The face shield, if applicable, is tested for penetration resistance by being shot in three spots along the centerline with an air rifle using a soft lead pellet weighing 1.0g with a diameter of 5.5mm at a velocity of approximately 500 kph. Penetration of the shield means failure.
A recent criterion is removability in an emergency. The helmet removability test determines whether the helmet can be removed from an unconscious victim without resorting to any buckles, clasps or other mechanisms which may be rendered non-functional by impact stresses. The helmet is placed on the largest appropriate complete ISO head form with all the closures and retention systems engaged.
A technician must remove the helmet from the head form using simple, common hand tools but without accessing any of the helmet mechanisms. The hand tools for this test are limited to shears, simple edged tools and flat bladed screw drivers. The operation must not require more than thirty seconds.
Post-testing disassembly and inspection is also performed on at least one of a set of sample helmets that have passed all the foregoing tests. If structural failures that are “not plausible for inclusion in a production helmet” the model will be rejected, despite having passed the tests.
These are the helmet performance standards you are most likely to encounter in shopping for a helmet these days. They are fairly complex in their details, but fairly simple in their common goal: to give you the best protection from potentially devastating head injuries possible. Now all you have to do is decide which one(s) is best for what you need your helmet to do.
Reference: Snell Memorial Foundation, http://www.smf.org/